Image 1
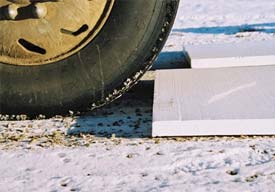
Layers of styrofoam are laid out on a compacted surface. The steering axle of diesel truck is rolled over the styrofoam. The weight of truck supported by the two tires is about 11,000 lbs. |
|
Image 2
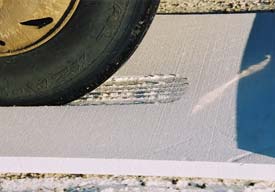
The styrofoam compressed to about 50% of it’s original thickness as the tires rolled the weight of the truck forward. |
|
Image 3 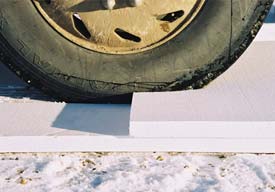
An additional sheet of styrofoam was installed to simulate softer conditions. |
|
Image 4
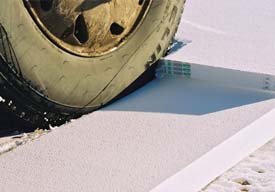
A third layer was added to simulate softer conditions. |
|
Image 5 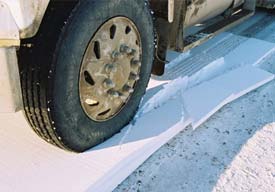
The weight of the truck was distributed onto the surface area of tires where it meets the underlying ground. Each square inch of tire with contact with the underlying material carried about 114 lbs of weight. The thicker layers of Styrofoam also recovered once the weight was removed. This would likely not be the case with soil. You will also notice that the weight on the underlying material is vertical and does not illustrate any signs of horizontal compression. |
|
Image 6
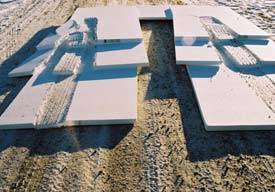
The elastic characteristics of the styrofoam resulted in some recovery once the load was removed. This would likely not be as predominate in soft or non compacted soils. |
|
Image 7
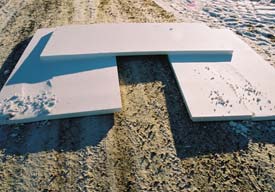
This is the bottom layer of the three layer section of the test track. The weight of the load caused compression with this layer. This indicates a load will sink in soft or non compressed soil until it reaches a foundation or a balance point where the weight is exerted onto the contact area of the tire can be supported by the underlying ground. In this case, the foundation was the compacted ground located beneath of the styrofoam. |
|
|